SmartJet™ – Emulsion selection
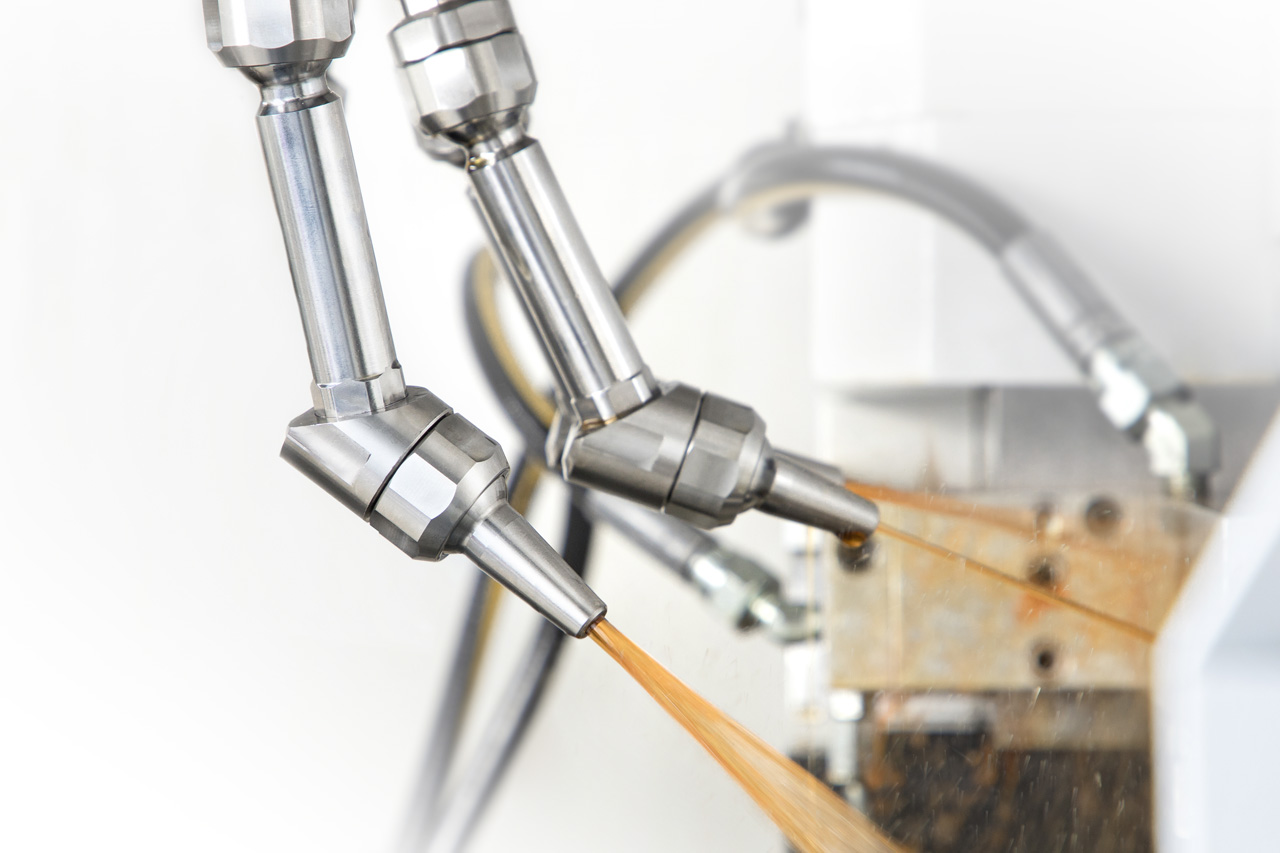
Emulsions are widely used in metalworking applications to improve the performance of cutting and grinding fluids. An emulsion is a mixture of two immiscible liquids, typically oil and water, stabilized by an emulsifier. In metalworking applications using SmartJet™, the emulsion is typically directed into the process using air pressure to improve the flow rate and coverage. In this article, we will provide general guidance on selecting an emulsion suitable for optimal work with the SmartJet™ in metalworking applications.
Selection of Base Fluids:
The first step in formulating an emulsion is to select the base fluids. The base fluids should be carefully chosen to ensure they are compatible and provide the desired performance. In metalworking applications, mineral synthetic oil and water are commonly used as the base fluids. Synthetic oil is preferred because of its lubricating properties, while water is used for its cooling properties.
Selection of Emulsifier:
The second step in formulating an emulsion is to select the emulsifier. The emulsifier is a crucial component of the emulsion because it helps to stabilize the mixture and prevent separation. There are different types of emulsifiers available, including anionic, cationic, and non-ionic emulsifiers. In metalworking applications, non-ionic emulsifiers are preferred because they are more stable and compatible with a wide range of base fluids.
Emulsion Concentration:
The concentration of the emulsion is an important factor in its performance. The concentration is typically expressed as a percentage of the total volume of the emulsion. In metalworking applications, emulsions with a concentration of 5-15% are common. The concentration should be carefully selected based on the desired performance and the application requirements.
Mixing Procedure:
The mixing procedure is also an important factor in the formulation of an emulsion. The emulsifier should be added to the base fluid slowly while stirring. The mixture should be agitated until the emulsifier is completely dissolved. The emulsifier should be added in the recommended dosage to ensure the stability of the emulsion. Once the emulsifier is dissolved, the emulsion should be mixed using a high-speed mixer until it is homogeneous.
pH of Emulsion:
The pH of the emulsion is also an important factor in its performance. The pH should be carefully controlled to ensure it is within the desired range. In metalworking applications, the pH of the emulsion is typically between 8 and 9. The pH can be adjusted using a pH buffer solution. The pH buffer solution should be added slowly while monitoring the pH until it reaches the desired range.
Selection of Additives:
Additives can be added to the emulsion to improve its performance. Additives can provide additional lubrication, improve the cooling properties, and reduce the foaming of the emulsion. The selection of additives should be based on the application requirements and the desired performance.
Air Pressure:
The air pressure should be carefully controlled to ensure the emulsion is delivered at the desired flow rate and coverage. The air pressure can be adjusted using a pressure regulator.
In summary, the formula for creating an effective emulsion for metalworking applications using SmartJet™ involves the careful selection of base fluids, emulsifiers, and additives, as well as the control of emulsion concentration, pH, and air pressure. The emulsion should be carefully mixed using a high-speed mixer until it is homogeneous. The emulsion can then be delivered to the metalworking process using SmartJet™ to improve the flow rate and coverage.
It is recommended to consult with an emulsion supplier or metalworking specialist to select an emulsion that is suitable for your specific application and process requirements. They can provide guidance on selecting the appropriate emulsion and ensure that it is compatible with SmartJet™ needs.