SmartJet™ – Chip removal
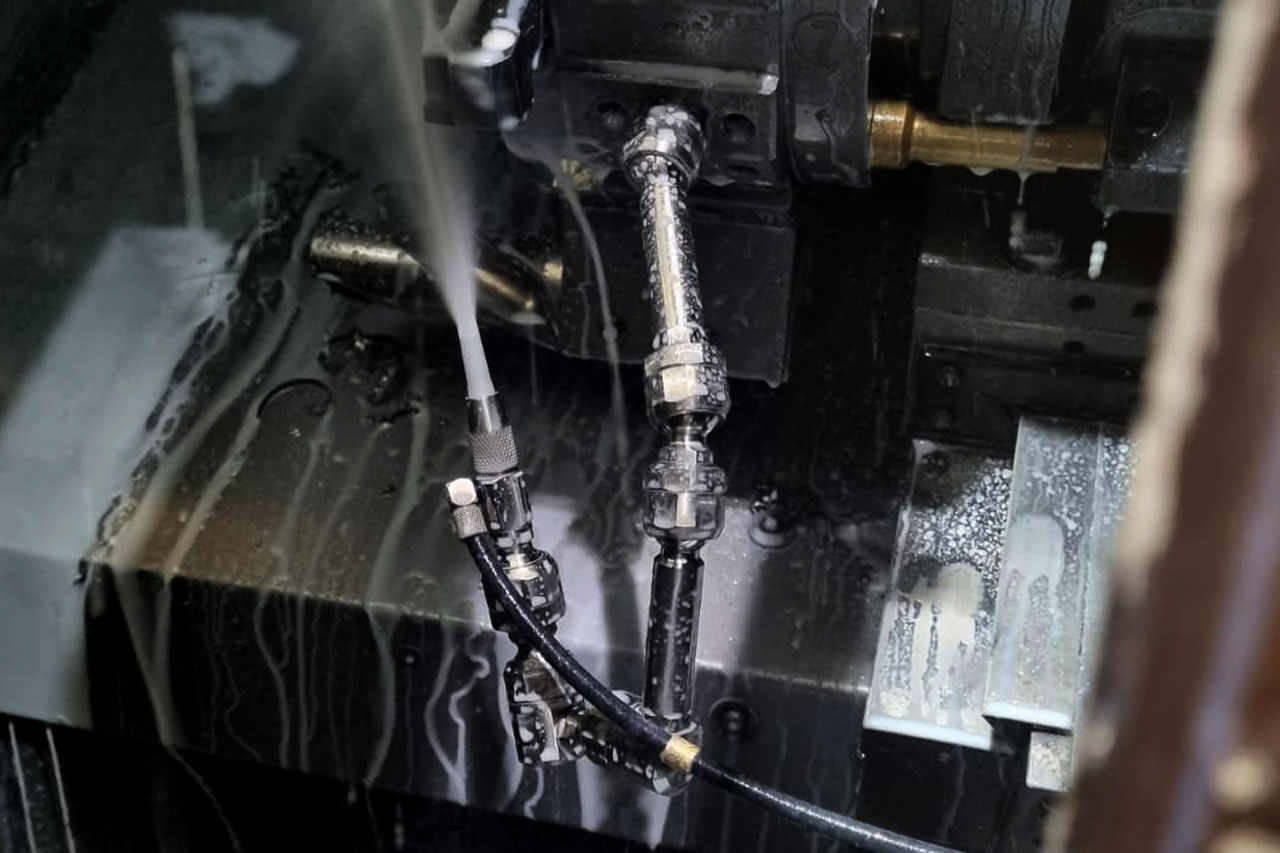
Metalworking processes are an essential part of many industries, ranging from aerospace to construction. The processes involve cutting, shaping, and forming metallic materials to create various components and products. During these operations, chips or small pieces of the metal are formed as the cutting tool removes material. These chips can cause several issues if not cleared immediately, affecting the quality of the workpiece, and damaging the cutting tool. Therefore, it is crucial to clear the chips promptly after their formation to ensure that the machining operation proceeds efficiently.
The primary reason for clearing chips immediately is to prevent them from recutting and interfering with the tool’s performance. When the cutting tool encounters chips left in the workpiece, it can push them into the surface, causing damage, and reducing the tool’s lifespan. This effect is particularly common when using tools with multiple flutes, where the chips can get trapped between the flutes, causing friction and heat buildup. As a result, the cutting tool can overheat, leading to premature wear or even catastrophic failure.
Clearing chips immediately also helps to maintain the quality of the workpiece by reducing the chances of surface defects such as burrs, scratches, and roughness. These defects can be caused by the recutting of chips or the accumulation of chips on the surface of the workpiece. Chips can also cause interruptions in the cutting process, leading to variations in the cutting force, which can cause dimensional inaccuracies in the workpiece. Therefore, clearing chips immediately after formation is essential to ensure that the machining operation proceeds efficiently, with minimal interference and high precision.
One of the most effective ways of clearing chips in metalworking processes is through the use of coolants or cutting fluids, which are applied to the cutting tool and the workpiece during the operation. Coolants help to lubricate the cutting tool and workpiece, reducing friction and heat buildup, which can cause premature tool wear and workpiece damage. They also help to flush away chips from the cutting zone, preventing recutting and reducing the chances of surface defects.
Emulsions are a type of coolant commonly used in metalworking processes due to their versatility and effectiveness. Emulsions are made up of oil and water, with additives such as surfactants, rust inhibitors, and biocides. The emulsion’s composition can be adjusted to suit specific machining operations, such as cutting speed, tool material, and workpiece material. When applied to the cutting zone, the emulsion helps to reduce the cutting temperature, lubricate the tool, and flush away chips from the workpiece.
However, emulsions alone may not be sufficient to clear chips effectively, especially when machining deep holes or narrow slots, where the chips can get trapped and cause recutting. Therefore, a combination of emulsion and air pressure can dramatically improve chip dispersion and clearing.
Air pressure, also known as chip evacuation, is a method of using compressed air to blow chips away from the cutting zone. Air pressure is particularly effective when dealing with long, stringy chips that may not be easily flushed away by emulsions. When air pressure is applied, the chips are blown out of the cutting zone, preventing recutting, and reducing the chances of interference with the tool or the workpiece. Air pressure can be applied through various methods, such as through the spindle of the machine, through dedicated air nozzles, or through the cutting tool itself. Using the SmartJet™ we are able to provide the air pressure at the most precise and correct point without adversely affecting the flow of the coolant.
When emulsion and air pressure are used together, the benefits of both methods are combined, resulting in a highly effective chip clearing system. The emulsion helps to lubricate the cutting tool and workpiece, reducing friction and heat buildup, while the air pressure blows the chips away from the cutting zone, preventing recutting and reducing the chances of interference. The combination of emulsion and air pressure also helps to reduce the overall machining time, as the process of clearing chips is faster and more efficient, allowing for higher productivity and throughput.
To achieve the best results with a combination of emulsion and air pressure, it is crucial to optimize the parameters of the machining operation. This includes adjusting the emulsion concentration, the air pressure, the cutting speed, and the feed rate. These parameters should be optimized for the specific workpiece material, cutting tool, and machining operation to ensure that the chip clearing system is effective and efficient.
In conclusion, clearing chips immediately after their formation is essential in metalworking processes to maintain the quality of the workpiece, prevent damage to the cutting tool, and ensure efficient machining operations. Emulsions are a popular coolant used in metalworking processes, but they may not be sufficient on their own to clear chips effectively, especially in deep holes or narrow slots. A combination of emulsion and air pressure as perfectly used in SmartJet™ is highly effective in clearing chips, preventing recutting, reducing interference, and improving productivity. By optimizing the parameters of the machining operation, metalworkers can achieve the best results with this chip clearing system, leading to high-quality workpieces, longer tool lifespan, and improved efficiency.
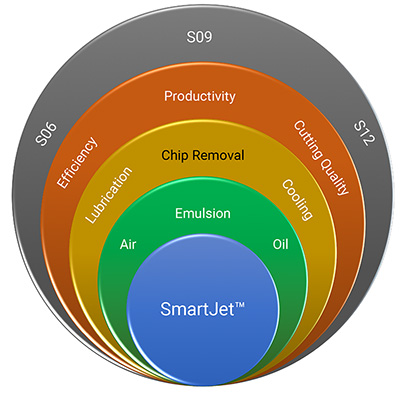