SmartJet™ – Aerosols
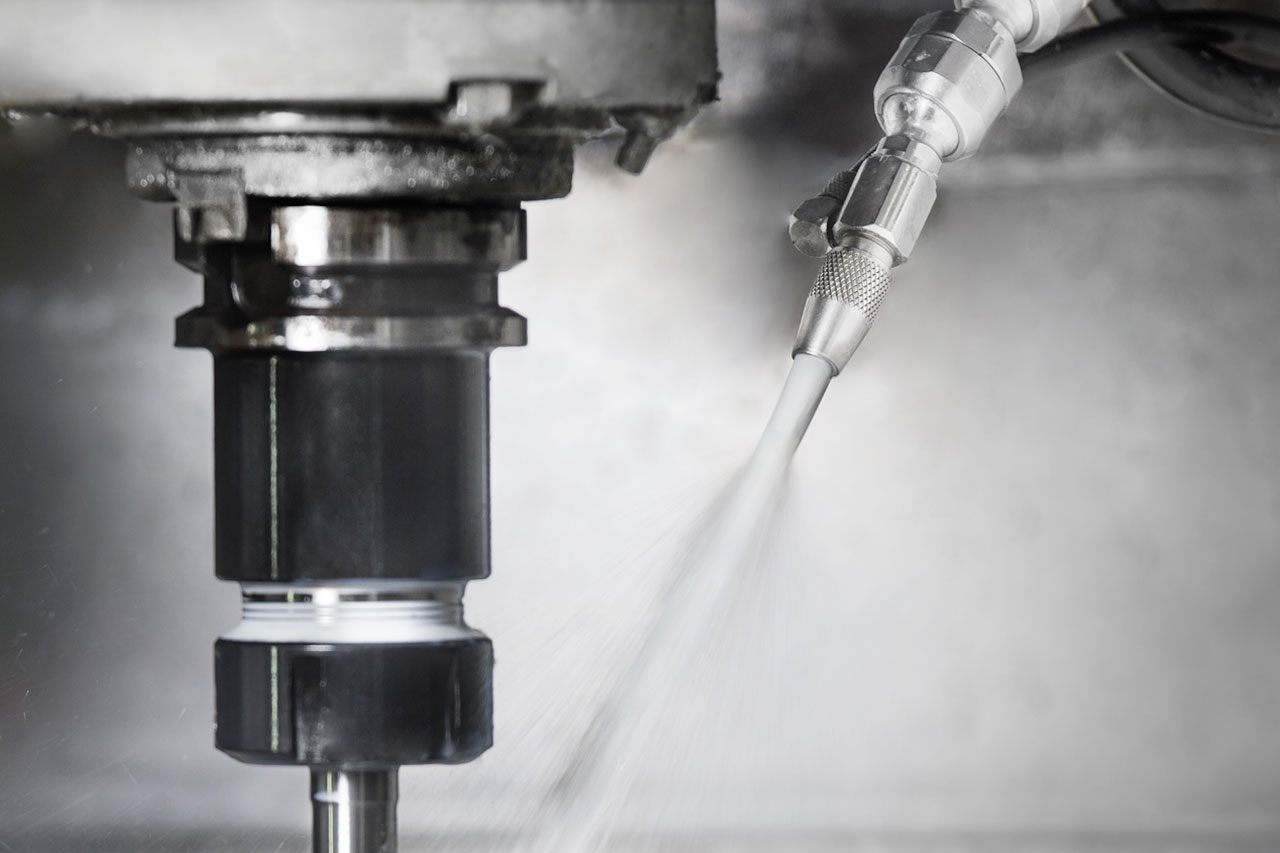
When air pressure meets a thin liquid, such as water, at high speed, it can result in the formation of aerosols. Aerosols are small particles of liquid or solid suspended in the air. These particles are formed when the air pressure forces the liquid into small droplets, which are then carried away by the air. The process of creating aerosols is called atomization, and it is commonly used in a wide range of applications, including industrial processes, medical procedures, and even in everyday life.
Maximum speed of air:
The maximum speed that air can reach when creating aerosols depends on several factors, including the pressure of the air, the density of the liquid, and the size of the orifice used to create the aerosols.
The pressure of the air is the most critical factor that determines the maximum speed of air. The higher the air pressure, the faster the air can move. However, there is a limit to how fast the air can move, and this limit is determined by the speed of sound. The speed of sound is the maximum speed that a pressure wave can travel through a medium, such as air. The speed of sound in air at room temperature is around 340 meters per second (m/s). Therefore, the maximum speed that air can reach when creating aerosols is around 340 m/s (1 Mach).
The density of the liquid is also a crucial factor that affects the maximum speed of air. The denser the liquid, the harder it is for the air to force it into droplets, and the lower the maximum speed of air. For example, water has a higher density than alcohol, so it is more challenging to create aerosols from water than from alcohol.
The size of the Jet or orifice used to create the aerosols also affects the maximum speed of air. The smaller the Jet or orifice, the higher the air pressure required to create aerosols, and the higher the maximum speed of air. However, there is also a limit to how small the Jet or orifice can be before the air pressure required becomes too high to be practical.
Relationship between the speed of air, liquid, and aerosols:
The speed of the aerosols created when air pressure meets a thin liquid depends on several factors, including the speed of the air, the speed of the liquid, and the size of the droplets.
The speed of the aerosols is typically lower than the speed of the air due to the drag force caused by the interaction between the aerosols and the surrounding air. The drag force is proportional to the square of the speed of the aerosols and increases rapidly as the speed of the aerosols increases. Therefore, as the aerosols move away from the source, their speed gradually decreases due to the drag force.
The speed of the liquid also affects the speed of the aerosols. The faster the liquid moves (as in SmartJet™) the more energy it has, and the smaller the droplets it can form. Smaller droplets have less mass, so they are easier to carry away by the air, resulting in faster-moving aerosols.
The size of the droplets also affects the speed of the aerosols. Smaller droplets have less mass, so they are easier to carry away by the air, resulting in faster-moving aerosols. However, smaller droplets also have a larger surface area per unit volume, which makes them more susceptible to evaporation and can cause them to dry out before they reach their destination.
Atomization can be used as a coolant in metal cutting applications. Metal cutting involves removing material from a workpiece using cutting tools, which can generate a lot of heat due to friction and deformation of the material. The heat generated can cause damage to the cutting tool and the workpiece, resulting in reduced tool life, poor surface finish, and dimensional inaccuracies.
Atomized coolants are used to reduce the heat generated during the cutting process by spraying a combination of emulsion, air and aerosols onto the cutting tool and the workpiece. The coolant absorbs the heat generated and carries it away from the cutting zone, reducing the temperature and improving the efficiency and accuracy of the cutting process.
Atomized coolants are typically used in high-speed machining applications, where the cutting tools operate at high speeds and generate a lot of heat. The use of atomized coolants can also improve the quality and consistency of the surface finish by reducing the formation of burrs and improving chip evacuation.
There are several advantages of using atomized coolants in metal cutting applications. Firstly, they can significantly reduce the temperature in the cutting zone, which can prolong the life of the cutting tool and improve the surface finish of the workpiece. Secondly, they can improve chip evacuation, resulting in better cutting efficiency and reducing the risk of chip buildup and tool damage. Thirdly, they can reduce the amount of fluid used, which can be more cost-effective and environmentally friendly compared to traditional coolant systems.
In conclusion, the use of atomized coolants jets in SmartJet™ units in metal cutting applications can significantly improve the efficiency, accuracy, and quality of the cutting process. They can reduce the temperature in the cutting zone, improve chip evacuation, and reduce the amount of fluid used. Understanding the factors that affect atomization, such as the air pressure, the density of the coolant, and the size of the jet, can help optimize the cooling process and improve the performance of metal cutting applications.